Metal Aerogels
Until very recently, metal aerogels did not exist. This is partly because there were (and still are) no known synthetic routes for producing wet gels of metals, although numerous synthetic routes for preparing solutions of metal nanoparticles (sols) do exist. In principle, if a gel composed of a network of metal nanoparticles could be prepared, it could also be supercritically dried to produce a metal aerogel. This said, like enlightenment and entropy, aerogel is a state function-it doesn’t matter how you get there but just that you do. The most consistent definition of aerogel implies that for a material to qualify as an aerogel, it must possess no less than 50% liquid-free porosity by volume and must be primarily mesoporous.
Just a quick note before we go any farther–if you read about “silicon aerogels” or “aluminum aerogels” on the web, these are almost certainly typos or misrepresentations of silica aerogels and alumina aerogels, respectively, and not really metal aerogels.
There are now a number of ways to make nanoporous metal foams that almost fit both criteria, however, and one way that unambiguously fits both. Here we will discuss the three major approaches:
- Combustion Synthesis of Metal Nanofoams
- Dealloying of Templated Au Alloys, and
- Nanosmelting of Iron Aerogels
What’s the Big Deal About Metal Aerogels?
Metal aerogels are potentially invaluable materials because they combine the unique properties of metals with the unique properties of aerogels. First, they would exhibit high specific surface areas (100-500 m2 g-1) and would be electrically conductive. This combination would make them valuable for applications where high-surface-area electrodes are needed, such as supercapacitors (sometimes called ultracapacitors), fuel cells, batteries, and water desalination. Secondly, nanosized particles of metals have been shown to exhibit enhanced catalytic activity overt bulk forms of the same metal. Gold, in fact, is very uncatalytic in the bulk, while gold nanoparticles very efficiently catalyze all sorts of nifty reactions, including room-temperature oxidation of carbon monoxide to carbon dioxide and carbon nanotube growth. Since metal aerogels would be composed of a three-dimensional network of nanosized metal particles, metal aerogels would thus be useful for making efficient, lightweight catalytic converters and useful in serving as catalytic substrates for other chemical reactions. Moreover, this means that metals like Fe or Ni could one day replace Pd, Rh, and Pt in catalytic converters, which are expensive and in diminishing supply.
A couple specifically sexy possibilities:
- Hydrogen Storage. Palladium, magnesium, nickel, and lanthanum aerogels could provide the ultimate scaffoldings for rapid uptake and release of hydrogen storage. Current hydrogen storage technologies have the problem that they can rapidly uptake hydrogen by forming a metal hydride, but it takes a long time to release the hydrogen back of the metal (which makes them not suitable for cars). But since just like you can only walk halfway into a forest before walking out of it, the thin struts of a metal aerogel potentially make for rapid hydrogen release, improved heat conduction, and thus safe hydrogen storage for cars.
- Antimicrobial Scaffolds. Silver aerogels could be incorporated in biomedical implants to provide a quasi-permanent antimicrobial functionality that doubles as a structural element.
- Irregularly-Shaped Magnetic Media. Extending the advantages of thin film metals to a 3-D materialy, magnetic metal aerogels could be useful for applications ranging from data storage to flat-panel speakers.
- X-Ray Optics. Metal aerogels with regular pore structures would enable production of optics for X-ray systems including functional X-ray lenses (think an X-ray microscope).
Metal Nanofoams from Combustion Synthesis
In 2005, Dr. Bryce Tappan, Dr. Steve Son, and colleagues at Los Alamos National Laboratory developed a method for producing a class of nanoporous metal foams (or “nanofoams”) which exhibit aerogel-like characteristics. The story goes something like this. Tappan was working with energetic transition metal complexes in which a transition metal atom is bound to one or more bis(tetrazolato)amine (also called bistetrazoleamine or BTA) ligands. These compounds were originally intended for use in low-smoke colored pyrotechnics, since many transition metals produce colorful emissions when burned (as in fireworks).
One day, Tappan was investigating the way these compounds burn by igniting pressed pellets of the compounds with a hot wire in a pressure vessel filled with argon at a pressure of 300 psi, (20.4 atm, 2.067 MPa) To his surprise, instead of vaporizing, an extruded foamy material-not unlike the carbon snakes you’d light off on the Fourth of July-remained after combustion.
Analysis of these foams revealed they were approximately 50% metal/50% residual organics by weight and, although they appeared to be largely macroporous (meaning they have micron-sized pores), they exhibited significant mesoporosity (like an aerogel). BTA complexes of iron, cobalt, nickel, copper, and numerous other metals all resulted in similar so-called “nanofoams” through the same combustion synthesis method. It was later found that a straightforward high-temperature treatment of the foams under a hydrogen atmosphere could be used to remove the residual organics from the foams, leaving behind purified, high-surface-area (~50-200 m2 g-1) metal nanofoams.
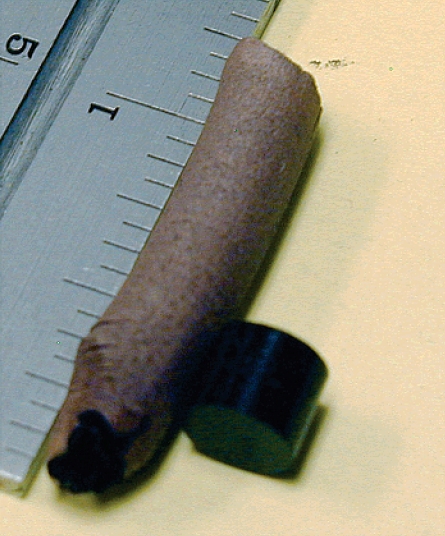
Iron nanofoam (long gray foam) next to an unburnt FeBTA pellet (image courtsey of Dr. Bryce Tappan, Los Alamos National Laboratory).
All of the nanofoams have very low densities, generally much less than 1 g cm-3 (that is, less than the density of water)-significantly less than the density of their bulk metal form. Nanofoams vary greatly in their mechanical properties depending on the element of which they are composed. Copper nanofoams as-produced, for example, are remarkably robust, can be bent, and are very easy to handle. Iron nanofoams as-produced, on the other hand, are quite ashy, almost like burnt paper, and must be handled delicately until they can be annealed to give them more strength.
Tappan and colleagues have produced a wide array of nanofoams since their original discovery in 2005 including nanofoams of silver and gold. Silver nanofoams are of interest for their antimicrobial properties, and gold nanofoams for their potentially high catalytic activity and plasmonic resonance.
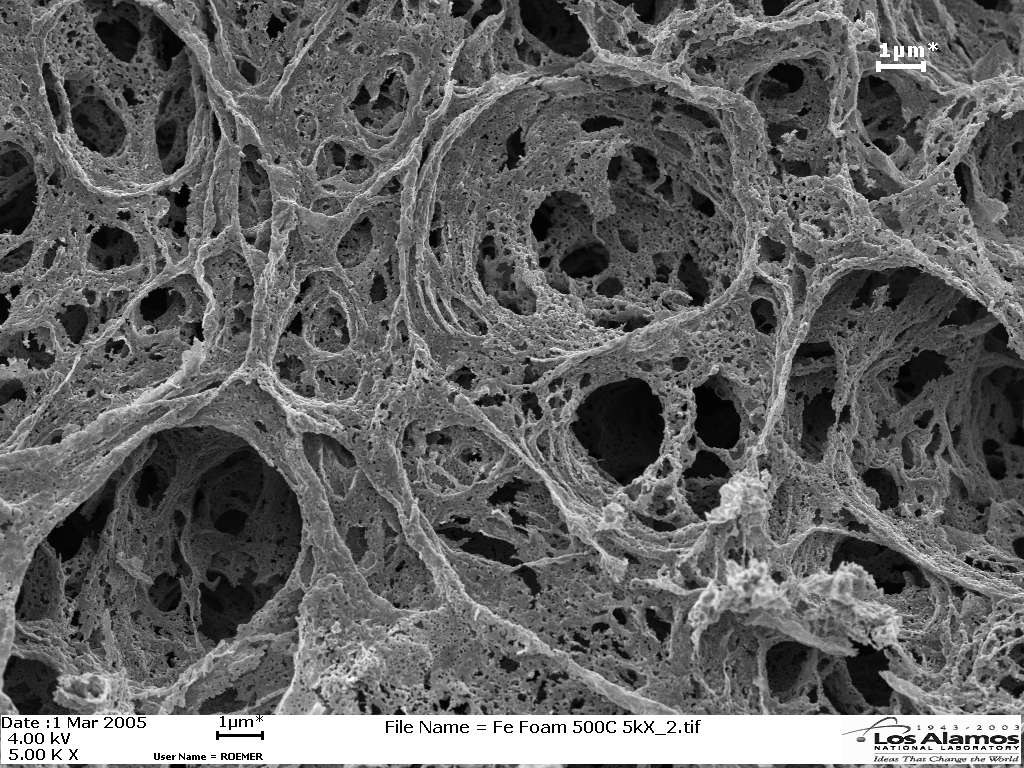
Scanning electron microscope image of an iron nanofoam (image courtesy of Dr. Bryce Tappan, Los Alamos National Laboratory).
How Metal Nanofoams Are Made
WARNING: Production of metal nanofoams involves the synthesis and ignition of energetic materials. While many metal bis(tetrazolato)amine complexes are only mildly energetic, some can be very dangerous! This type of chemistry should not be performed by an amateur and requires proper training in energetic materials synthesis, proper facilities, and safety precautions.
Process Overview
To produce a metal nanofoam, energetic metal bis(tetrazolato)amine (BTA) complexes are synthesized, compressed into cakes, and ignited in an inert atmosphere. The self-assembled nanoporous foam results from the action of heat released from combustion of the energetic complexes causing rapid gas-phase metal nanoparticle nucleation and agglomeration combined with the decomposition of the nitrogen-rich BTA ligands into gaseous products which, in effect, serve as a nano-blowing agent.
Synthesis of Bis(tetrazolato)amine (BTA) Complexes
BTA ligands can be produced by the method described by Naud et al. Briefly, sodium dicyanoamide is reacted with sodium azide acidified to a pKa of less than 1 to produce sodium bis(tetrazolato)amine (Na-BTA). The Na-BTA is then rinsed thoroughly with sodium nitrite (NaNO2) to destroy any residual azides. Na-BTA is then treated with HCl to produce the free acid bis(tetrazolato)amine monohydrate (BTAw) which is then recrystallized. BTAw is subsequently treated with 3-4 equivalents of ammonium hydroxide to produce a highly-soluble diammonium salt (DA-BTA) which yields a chalky white precipitate diammonium bis(tetrazolato)amine monohydrate (DA-BTAw) upon evaporation.
DA-BTAw can then be reacted with any of a number of metal chloride, nitrate, or perchlorate salts in aqueous solution to form the desired metal-BTA complex. The number of BTA ligands which attach to the metal center depends on the chemistry of the metal being used. For example, reaction of DA-BTA with iron perchlorate (a dangerous oxidizer) gives an iron complex with three BTA ligands. Reaction of DA-BTA with auric acid (HAuCl4) gives two complexes, one with two ligands and one with three.
The resulting metal complex can then be isolated, washed, and purified.
Self-Propagating Combustion Synthesis of Metal Foams
Before ignition, complexes are pressed at a gauge pressure of 179 kPa to yield pellets of approximately 95% theoretical maximum density. The pellets are then placed in a high-pressure combustion chamber and the chamber filled with an overpressure of an inert gas such as argon or nitrogen. A pressure of 300-1000 psi is generally used. This pressure will affect the microscopic morphology of the foam which will result. Finally, the complex is ignited by contacting with a resistively heated nickel-chromium (Ni-chrome) wire. In just about one second, the complex ignites and a combustion front propagates across the pellet. The pellet expands in volume and the nanoporous metal foam forms. The pressure vessel is then depressurized into a ventilated exhaust trunk (as it contains toxic gaseous by-products), flushed with inert gas, and then opened.
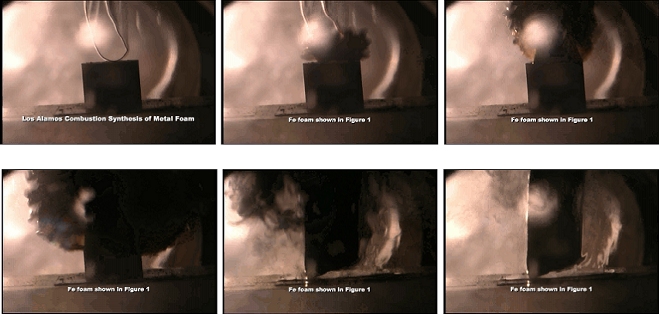
Video stills from ignition of FeBTA in the production of Fe nanofoam (stills courtesy of Dr. Bryce Tappan, Los Alamos National Laboratory).
Advantages and Disadvantages of Metal Nanofoams Produced through Combustion Synthesis
Combustion synthesis of metal nanofoams offers a number of unique advantages, including:
- Works for many main group, transition, lanthanide, and actinide metals
- Scalability
- Not restricted by diffusion-limited steps such as solvent exchange
- Tailorability of pore size
- Tailorability of foam strength
- Tailorability of electrical conductivity
- Fe, Co, and Ni nanofoams can be made magnetic
Some disadvantages:
- Requires synthesis and ignition of energetic materials
- Some metal nanofoams are quite ashy and require annealing to be handleable
- Attaining additional mesoporosity and microporosity requires chemical or vapor etching
Future Work
Synthesis of lots of different types of metal nanofoams is underway, along with methods for shape control and pore size control.
Dealloying of Templated Au Alloys
One method for making nanoporous metals is called dealloying. In this method, an alloy of gold and a less-noble (more reactive) metal is prepared (usually an alloy of copper and gold or silver and gold), where enough less-noble metal is present in the alloy that it forms a continuous percolating network throughout the gold. The alloy is then etched electrochemically to selectively remove the less-noble metal from the gold, leaving behind a porous gold framework. Dealloying can also be done chemically using acids. Generally, though, this only works for thin (<1 mm) films, since the etching of the metal is diffusion-limited and the width of the resulting path for etching into alloy is only nanometers wide.
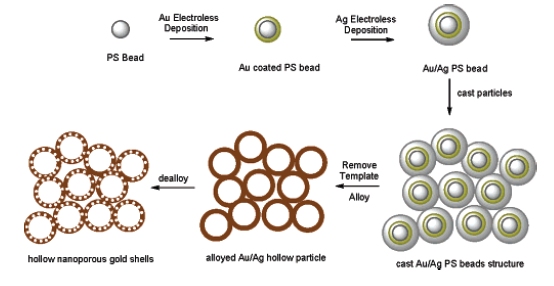
Synthesis of hierarchically porous Au foams by templating and dealloying (reprinted with permission from Gregory W. Nyce, Joel R. Hayes, Alex V. Hamza, Joe H. Satcher Jr., "Synthesis and Characterization of Hierarchical Porous Gold Materials", Chemistry of Materials, 19, 344-346 (2007). Copyright 2007 American Chemical Society).
Dr. Greg Nyce and Dr. Juergen Biener at Lawrence Livermore National Laboratory have developed a technique for making large monoliths of nanoporous gold foams through dealloying by addressing the diffusion problem. In their technique, gold (15 atomic %) and silver (85 atomic %) are deposited over micron-sized polystyrene spheres. The spheres are then cast into a container by pouring a suspension of spheres over filter paper. The polystyrene spheres then pyrolyzed away under inert atmosphere at 400°C, leaving behind a macroporous gold-silver foam. The gold-silver foam is then dealloyed, resulting in a hierarchically-porous gold foam-that is, a macroporous foam with nanoporous gold walls.
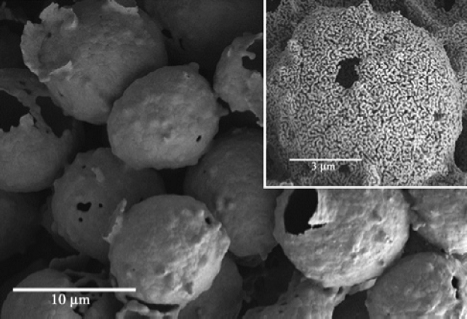
Scanning electron microscope image of templated gold-silver foam before dealloying (main picture) and after (inset). Dealloying creates nanoporosity in the material (reprinted with permission from Gregory W. Nyce, Joel R. Hayes, Alex V. Hamza, Joe H. Satcher Jr., "Synthesis and Characterization of Hierarchical Porous Gold Materials", Chemistry of Materials, 19, 344-346 (2007). Copyright 2007 American Chemical Society).
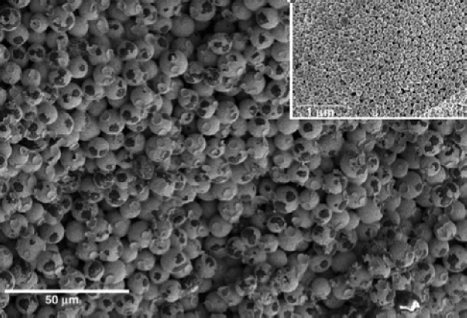
Scanning electron microscopy image filter-cast Au-Ag foam (reprinted with permission from Gregory W. Nyce, Joel R. Hayes, Alex V. Hamza, Joe H. Satcher Jr., "Synthesis and Characterization of Hierarchical Porous Gold Materials", Chemistry of Materials, 19, 344-346 (2007). Copyright 2007, the American Chemical Society).
Advantages and Disadvantages of Nanoporous Foams Made through Dealloying
The technique developed by Nyce and Biener has some great advantages:
- Allows for production of nanoporous gold foams with dimensions of several centimeters
- The foams can be used as substrates to enhance spectroscopy
- Foams can be made in any shape
- Relatively easy to make
Some disadvantages:
- Technique is generally limited to production of nanoporous gold foams and foams of a few other elements
- Pore size control is limited to the templating technique and the limitations of dealloying
Metal Aerogels through Nanosmelting of Hybrid RF-Metal Oxide Aerogels
In January 2009, Prof. Nicholas Leventis at the Missouri University of Science and Technology published the first synthesis of iron aerogels. His technique is the most direct analog to the techniques used for making other aerogels and results in materials which are highly mesoporous and exhibit the highest specific surface area reported for any nanoporous metal foam.
How Iron Aerogels Are Made
Iron aerogels are made through a nanosmelting process. They start out as a hybrid gel of resorcinol-formaldehyde (RF) polymer and iron oxide-effectively synthesizing an organic gel using the technique developed by Dr. Rick Pekala at Lawrence Livermore National Laboratory and an iron oxide gel using the technique developed by Dr. Alex Gash and Lawrence Livermore National Laboratory in the same mold at the same time. This hybrid RF-iron oxide gel is then supercritically dried to make a hybrid RF-iron oxide aerogel. Lastly, the aerogel is pyrolyzed under Ar at 800-1000°C. During this pyrolysis, the RF dehydrates to carbon (just like it does when you make carbon aerogels)-except for at these temperatures the resulting carbon then reacts with the iron oxide in the aerogel, pulling out oxygen to make CO2 and leaving behind Fe metal. This is the same process as smelting of iron oxide using coke (carbon) to produce pig iron, just at the nanoscale. The result is an aerogel of Fe with a little carbon left in it, effectively a “pig iron aerogel”, retaining only 33% of the mass of the original aerogel (the remaining 67% being RF polymer that dehydrated into the carbon that smelted the iron oxide to iron and, in the process, became carbon dioxide gas).
Fe aerogels are both magnetic and electrically conductive just like iron is. They have surface areas ranging from ~95 to 300 m2 g-1, and densities of about 0.046 g cm-3 (about 20 times less dense than water, and 172 times less dense than bulk Fe metal).
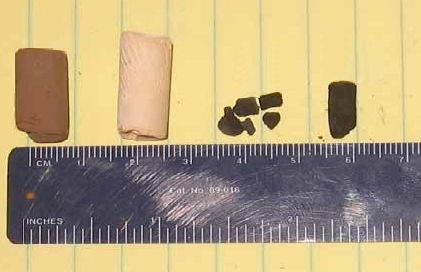
Hybrid RF-iron oxide aerogel (left), crosslinked RF-iron oxide aerogel (second from left), iron aerogel (second from right) made by pyrolysis of RF-iron oxide aerogel, iron/iron carbide aerogel (right) made by pyrolysis of crosslinked RF-iron oxide aerogel (image courtesy of Prof. Nicholas Leventis).
Advantages and Disadvantages to the Aerogel Nanosmelting Process
This technique has lots of exciting potential:
- Enables production of high-surface area iron aerogels
- Enables production of magnetic aerogels
- Allows for control over porosity
- Can vary composition from iron oxide to iron to iron carbide
- Uses existing aerogel production methods, chemicals, and equipment
- Potential allows for production of monoliths of any shape and large sizes
- Can be extended to many other metals
Some disadvantages:
- Requires diffusion-limited steps such as solvent exchanges (like other aerogels)
- Does not work for all metals, for example, metals like Au that don’t form stable bulk metal oxides or metals like Zr that can’t be smelted by carbon
- Shape control is very difficult as monoliths tend to shrink and crack upon pyrolyzing
Future Work
Aerogel needs you! This is one of the many areas of aerogel science where you can innovate. Aerogel.org looks forward to the world of new metal and metal carbide aerogels made possible through these exciting developments.